ПОЛИМЕРНЫЕ МОДИФИКАТОРЫ ДЛЯ КРОВЕЛЬНЫХ МАТЕРИАЛОВ
Кровли являются одним из основных ограждающих элементов зданий и сооружений. Состояние кровель, их долговечность является важнейшим социально-значимым фактором, от которого зависит многие стороны производственной и общественной деятельности, а также частной жизни человека. Мы поговорим сегодня о мягких кровельных материалах , даже о еще более узкой области – мягких рулонных материалах . На наш взгляд, значение использования полимеров в этой отрасли промышленности переоценить трудно. По существу, речь идет о подлинной революции, произошедшей в последние 10-15 лет.
Россия является самым крупным производителем и потребителем мягких кровельных материалов в Европе. Ежегодный объем их выпуска и потребления составляет более 640 млн.м2. В то же время до сих пор в структуре производства мягких кровельных материалов до 40% (в зависимости от региона) приходится на традиционные рубероидные. До начала 90х гг. в Российской Федерации производилось почти 1,5 млрд.кв.м рубероида в год. При производстве рубероида синтетические полимеры не используются.
Мягкие кровли , выполняемые из традиционных битумных материалов, сложны в устройстве: из-за специфических свойств битумов работы по наклейке многослойного рубероидного ковра выполняются сезонно, в основном, вручную, они не поддаются эффективной механизации. Низкие физико-механические, технологические и эксплуатационные показатели традиционных битумных кровельных материалов не обеспечивают надежной и долговечной защиты зданий, особенно эксплуатирующихся в таких специфических условиях, как химическая агрессия, климатические особенности севера и юга страны.
Затраты на эксплуатацию мягких кровель составляют от 5 до 12% общих расходов на все здание; более 40% повреждений зданий приходится на кровли. Ремонт рубероидных кровель, эксплуатирующихся на предприятиях химической, нефтеперерабатывающей, металлургической и других отраслей промышленности с агрессивными выбросами, обходится в 1,5 - 2 раза дороже устройства новых кровель.
По эффективности применения в строительстве рубероид занимает одно из последних мест среди строительных материалов, используемых в ограждающих конструкциях зданий и сооружений. Реальная долговечность зданий и сооружений составляет 60-100 лет, а средний срок службы рубероидных кровель - от 3 до 7 лет. Через 1-2 года эксплуатации протекает до 30% кровельных покрытий, к пяти годам ремонту подвергается 50 - 70%, к семи годам - 100% покрытий. На ремонт ежегодно расходуется более 50% валового выпуска мягких рулонных кровельных материалов.
Анализ отечественного и зарубежного опыта показывает, что решение проблемы технологичности устройства кровли, повышения ее надежности и долговечности в упомянутых эксплуатационных условиях может быть успешно осуществлено при использовании полимеров. Применение полимеров в сочетании с традиционными битумными материалами позволяет создавать новые эффективные материалы, отличающиеся повышенными физико-механическими и эксплуатационными показателями.
В настоящее время синтетические полимеры используются для улучшения свойств практически всех компонентов рулонных битуминозных материалов.
Наиболее существенно влияет на долговечность и большинство других эксплуатационных показателей материалов состав вяжущего (покровных слоев). Наличие полимерного модификатора придает вяжущему и всему материалу бОльшую теплостойкость и морозостойкость, эластичность, сопротивляемость усталостным нагрузкам, существенно (в несколько раз) повышает долговечность.
При производстве битумно-полимерных материалов для гидроизоляции кровли и фундаментов в России и странах СНГ, как впрочем, и в западноевропейских странах, в качестве полимерного модификатора битума в основном используются бутадиенстирольные блоксополимеры (СБС) и атактический полипропилен (АПП; последний – обычно в смеси с изотактической фракцией - ИПП).
Характерной особенностью поведения некоторых блочных сополимеров (рис.1) является, как известно, их способность проявлять, с одной стороны, свойства термопластов при повышенных температурах и низких скоростях сдвига и свойства эластомеров – при низких температурах и больших сдвиговых усилиях. Бутадиенстирольный блок-сополимер, кроме того, ограниченно растворяется в мальтенах битума: бутадиеновые блоки растворяются практически неограниченно, а стирольные способны лишь набухать, образуя термопластичные домены. При определенных концентрациях СБС ТЭП в надлежащим образом подобранном битуме в коллоидном расторе происходит обращение фаз, и матрицей становится полимерная фаза.
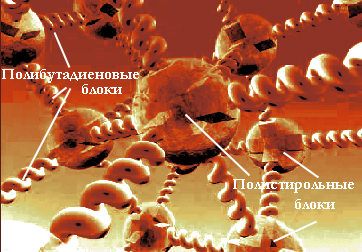
Благодаря этому смесь битума и полимера приобретает многие свойства полимера, в частности, эластичность, низкотемпературную гибкость и т.д..
Атактический полипропилен, равно как и другие аморфные полимеры, воздействуют на дисперсионную - мальтеновую среду битума, загущая ее, и через нее – на все свойства битума, упрочняя его, улучшая высокотемпературные свойства.
Иными словами, СБС-модификатор значительно улучшает низкотемпературные свойства битумов (значительно понижая температуру стеклования, Тст.) и несколько повышает температуру текучести (Тт.). АПП, напротив, значительно повышает Тт. и в гораздо меньшей степени понижает Тст. При этом интервалы пластичности (ИПл.) , т.е. разности между температурами текучести и стеклования, при введении обоих типов полимеров значительно увеличиваются по сравнению с “чистым” битумом. Однако имеется одно различие. На рис.2 видно, что “центр тяжести” ИПл. смеси битума с АПП приходится примерно на +45-50 град.С, т. е на повышенные температуры (с точки зрения средней температуры окружающего воздуха). В случае с СБС “центр тяжести” ИПл. находится при температуре +20-25 град.С, что гораздо более соответствует нашему климату.
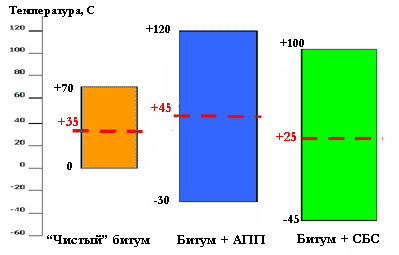
Ясно, чем ближе система к своим граничным условиям работоспособности, тем менее она устойчива.
Согласно данным многочисленных наблюдений, на большей части территории России открытые элементы покрытий зданий и сооружений работают в интервале температур от -60 до +80 град.С; при этом температурные деформации в стыках панелей и узлах сопряжений кровель могут достигать 4-6 мм. Такие деформации приводят к появлению мощных напряжений сдвига в нижнем (наплавляемом или мастичном) покровном слое рулонного материала, которые могут передаваться вышележащим слоям, приводя к появлению трещин, разрывов и других видам нарушений сплошности покрытия. В условиях континентального и резко-континентального климата , преобладающего на территории России, и связанных с этим значительными по амплитуде и частоте суточными и сезонными колебаниями температур, разрушающие воздействия на кровельные ковры более значительны, чем в странах с мягким климатом (например, в Италии).
Вследствие этого материалы с использованием СБС-термоэластопластов (Днепрофлекс, АйСиТекс, Гидростеклоизол© и др.) в большей степени соответствуют климатическим особенностям основной части территории России, в том числе регионов Центра, Сибири, Урала, Севера, в отличие от материалов с АПП, более пригодных в районах с теплым климатом (Юг России).
При правильном «районировании» битумно-полимерных кровельных материалов долговечность (срок межремонтной эксплуатации) кровель может достигать 20-25 и более лет; при ошибочном выборе материала долговечность покрытия будет примерно такой же, как и при использовании немодифицированного («простого») материала (например, рубемаста, бикроста, стеклоизол). При этом не следует забывать, что стоимость битумно-полимерного материала в несколько раз выше, чем стоимость «простого» стеклоизола.
Гидрол-Кровля©2009
При любом использовании материалов активная ссылка на сайт http://kgidrol.narod.ru обязательна